A new concept in manufacturing is the prospect of “Industry 4.0”. It’s a factory where the new technologies (automation, digital communication, Internet of Things, cloud, etc) are integrated into a complete production system.
The following YouTube video from Siemens makes it seem pretty real.
What does Industry 4.0 involve?
Most major industrial vendors and consultants have published serious statements about Industry 4.0 in the past few years. These are a sampling of their PDF summaries here:
- wC 2016 Survey
- Oracle 2016 Survey Report
- IBM Industry 4.0 and IoT Analysis
- McKinsey Update
- … and LOTs of others … just do a Google Search
Industry 4.0 describes the physical and IT building blocks for an end-to-end manufacturing system that requires far less human intervention. Definitions vary, but most are lists or descriptions of the technologies that will be used and supported. One of the most expansive lists is offered by McKinsey.
Where does video fit in?
Apparently, it doesn’t.
Mention of video technology is strikingly absent from the various industry definitions. As an exercise, try to find it in McKinsey’s chart. Video is a dynamically changing technology that is reshaping huge parts of the social landscape. Yet, it is not obvious in discussions of Industry 4.0. Take recent PDF whitepapers from the major consultants and do a text search for the term “video”. … pretty thin pickings!
I hope to write some articles about the possible role for video technology in Industry 4.0, but as a discussion starter, ask whether we will still need to see things in this shiny, digital factory … with our eyes, not just our sensors.
In other posts, I argue that we should use video to monitor and study business operations. Nowhere does it make more sense to me than in factories. However, I suspect that part of the reason we don’t see heavy video use now is because our factories are heavily staffed with human eyes and ears. Every manufacturing expert since Deming has tasked front line workers to be alert and recognize when odd events occur, so they can respond quickly and/or tell management. Good factories rely on the eyes and ears of its people to know what is happening. Video surveillance would certainly be useful, but companies can get by as long as the plant is fully and actively staffed.
Industry 4.0 expects to see a big reduction in plant floor headcount. That means there will be fewer eyes and ears. Look at this photo, taken in the Siemens plant in Amberg, Germany.
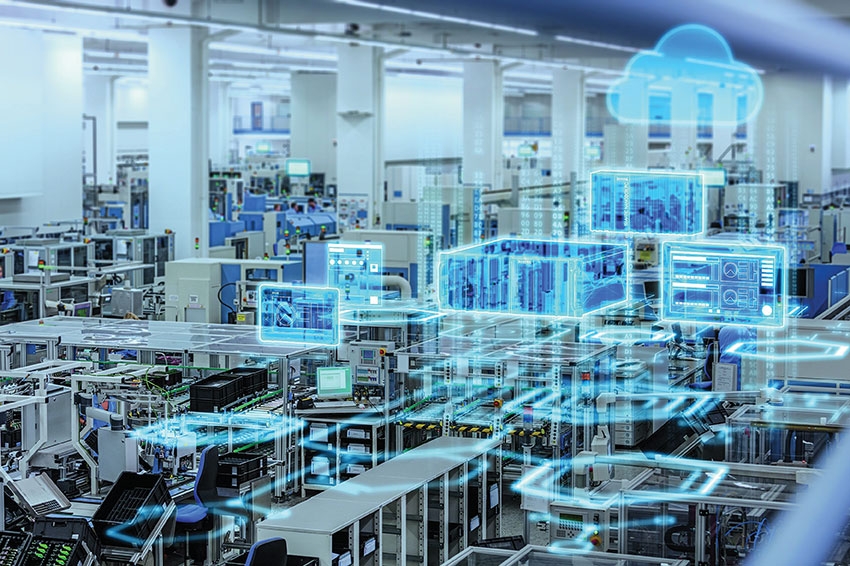
- How many people do you see?
- If something unexpected happens, what are the odds that staff will have seen and recognized it as it occurred?
The premise for Industry 4.0 assumes that sophisticated software controls will networked into every aspect of the operation. There will be tons of sensors, software and sophisticated diagnostics. The factory management software will recognize problems and respond much faster than humans could.
All of this assumes that the designers can anticipate the potential problems. If not, the limited staff will have to be detectives. They will have to piece together the root cause of each event … without the help of witnesses.
I expect it will work reasonably well for products that are hard-bodied, modular, discrete and easily tracked. In other words, I take Siemens at its word that it works for the electronic products that are made in the Siemens’ plant. That will also apply to a lot of products in automotive and aerospace industries. What about softer products like upholstery in an auto plant? What if there were a lot more bits and pieces that were harder to track … like fasteners? What about wires and stuff? What if the raw materials are harder to standardize? What if … ?
Maybe it’s just me, but I would love to have a robust video surveillance system watching this factory, both from a long view and with less expensive cameras in closeups of key machines and production steps. If we specified 200 cameras, including some 4K high def units, I think we could we could aim them at every point where a failure or issue might occur in this factory. We could record everything that happened, 24/7, with a rolling 2 or 3 week buffer.
How much would that cost? Hardware from a high-end vendor like Bosch would probably come in around $120 to $140K. Installation might be another $50K. Do you think that would cause heartburn for someone building a plant like this?
Me neither.