Industry has embraced continuous improvement for at least a century. Arguably, it started with Frederick Taylor and evolved to Six Sigma and beyond. There were many advances, and a few fads, in between. Still, Deming’s Plan-Do-Check-Act (PDCA) is a common refrain:
- Observe what’s happening so you can plan changes
- Do the improvements
- Check how they work
- Act by making adjustments.
But that’s hampered when humans can’t see complex processes very well.
The human eye and brain were evolved for other things … like recognizing threats. For example, humans see a small region that is clearly in focus. That’s our “foveal” vision. Everything else is our “peripheral” vision. When you “watch” something, you miss most of the detail. Try it yourself … focus on something across the room and note the area that is clearly in focus.
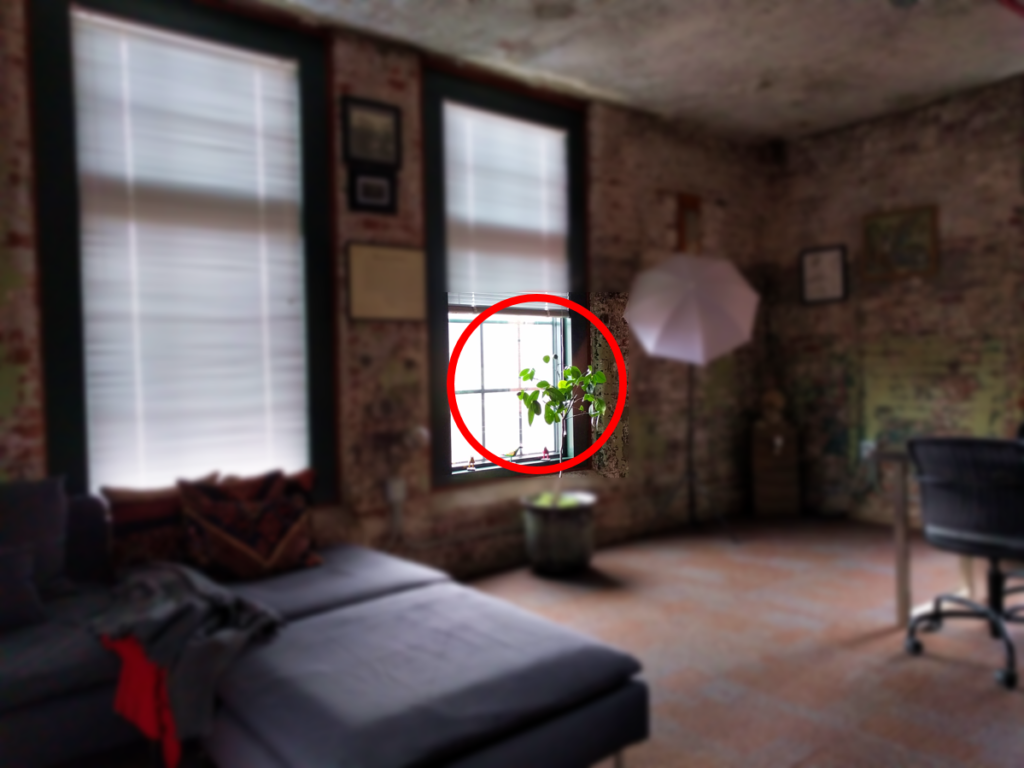
How can we really “watch” a complex activity? Our eyes flit from point to point and our brain struggles to tie the tidbits together. By Murphy’s law, the critical event will always happen wherever we aren’t looking at the moment and, of course, we won’t see clearly if something blocks our view.
Worse, our brains are flawed recorders. We lose interest and forget when the action is too slow. We can’t track and process when action is too fast. We struggle to hold competing viewpoints in focus and in sync. Even if we see it clearly and coherently, our memory will soon fail us on the details.
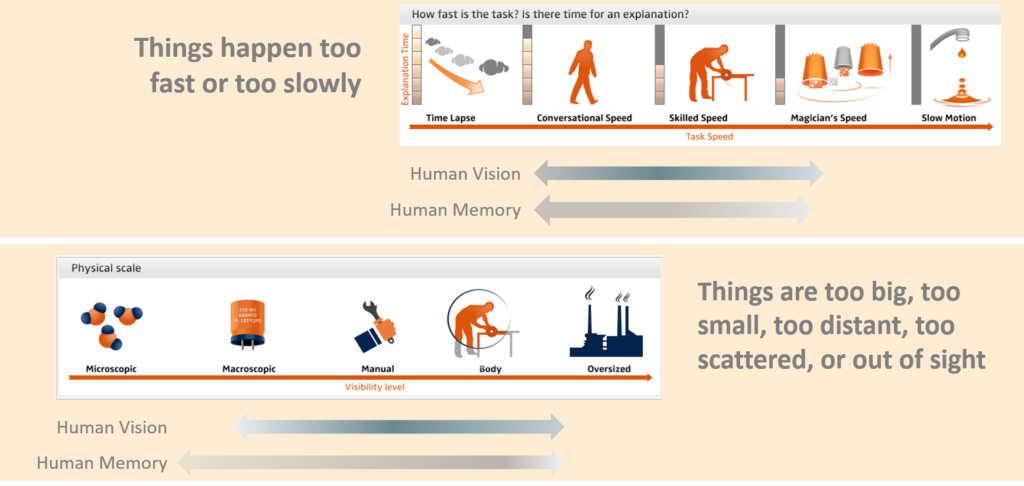
We know that process variations and anomalies are critical so we try to look for key details … but that makes it harder to remember and grasp the larger patterns. These limitations spurred operations experts to invent specialized analytical tools and techniques like SPC charts and Taguchi and adopt methods using “standard work” and SOPs. These are great tools, but they are band-aids to compensate for our human observational limitations.
What if we could see processes completely and remember them perfectly?
Recent advances in video security technology bring us closer to that reality. Virtually every business or production facility has a camera system to monitor comings and goings and they save the video for as long as they like.
Still, in the past 5 years, security video systems have improved amazingly:
- Camera resolution has improved at least 10 times.
- Camera prices fell at least 60% and storage costs even more.
- Software is smarter with web, IoT, cloud, machine learning and smart analytics
Those improvements and cost reductions promise a future where video systems routinely enhance our operational vision and memory. They would drive better decisions, support fairer evaluations, and enable faster and more precise discovery of root cause:
Imagine if we install ultra-HD cameras that overlap and collectively record everything happening across a large facility. Simultaneously, we install low-cost HD cameras at strategic operations like control panels, vulnerable equipment, error-prone manual tasks, and key inventory buffers. Then we record every camera.
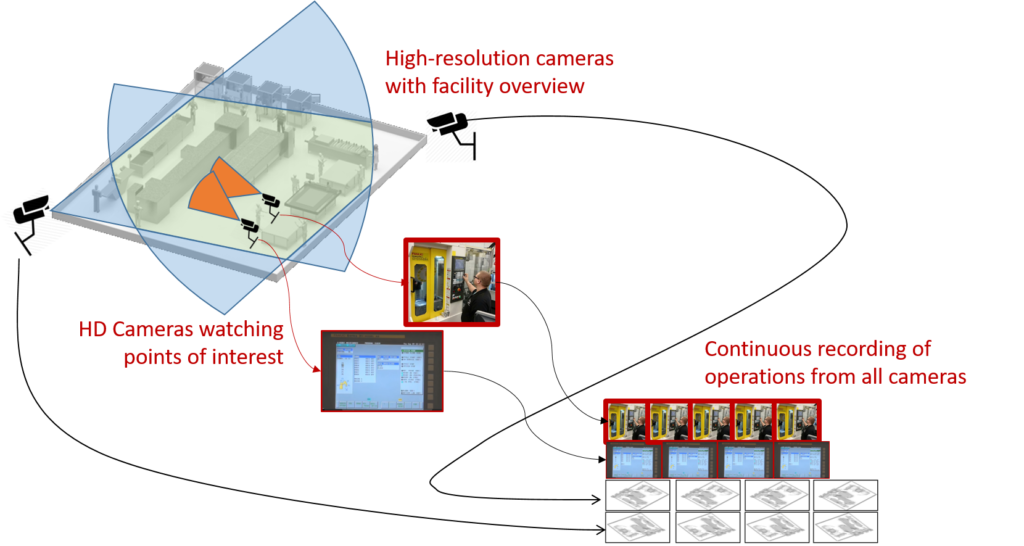
When we suspect we are seeing the effects of an earlier operational problem, we can search the wide shots with digital zoom and apply capabilities like the ones shown below. I am sure we will see further capabilities from sophisticated software and/or AI.
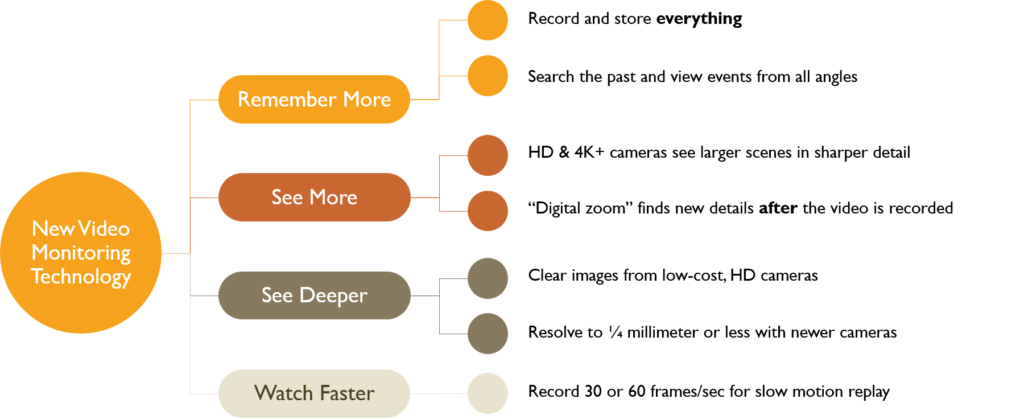
There’s a good chance we will see problems as they actually occurred days or weeks previously. At the least, we will know what was happening in the vicinity at the time. With a little foresight, we site the focused camera shots at key hot spots like control panels and key processing operations.
We can build systems like this today … creating a literal “time machine” to view events that happened anytime in our recorded history … likely from multiple camera angles. Professional sports has done this for years. They can review controversial goals, questionable fouls, or any other ambiguous play. Why shouldn’t business operations have a similar capability? The system designs are readily available and the costs are falling rapidly.
Why don’t we use video surveillance technology aggressively in operations?
I suspect that, until recently, security video technology really wasn’t good enough and, worse, it used a philosophical model didn’t quite fit. Security camera systems were originally designed so security staff could watch live video and “catch” bad behavior. No manager can afford to pay operations experts to watch TV monitors. They would be much better placed as live supervisors on the floor. Plus, if you embrace an empowered work culture, that kind of big brother approach is the last thing you want .
If managers focused on using to recorded video as a tool to analyze process behavior and plan process improvement, I think it would fit very well into a modern, empowered workplace. The key is not the technology, it will be how management chooses to use it.