Factories need time machines!
It would be really cool if a quality manager could go back in time and watch how (ultimately) defective units were made … their actual journey through production. It might help the maintenance engineer to watch a (later broken) machine as it started to give signals in the minutes and hours before it failed. It would be cool to go back and show everyone the big production screw-up and debrief how it happened and what can be done to prevent it in the future.
It’s not science-fiction!
It’s easy, inexpensive, familiar and poses no technical risk. Install a comprehensive video surveillance system and point the cameras at your operations (see my earlier blog posts here, here and here).
You can outfit a large production facility for less than $100K in hardware (services and usage labor will vary). In most facilities you won’t need expensive pan-tilt-zoom cameras or vandal-proof housings. Cheap Chinese-built commodity cameras might be OK. With a robust system, 50 to 100 HD or 4K resolution cameras can watch and continuously record pretty much everything that happens, with weeks or months of stored footage from each camera. If something arises, review the video footage to see what occurred. Your security staff does this every day. Police routinely do it to solve crimes. To be fair, you can’t change what happened, but you can easily go back and see what happened.
A time machine might look something like this.
High resolution cameras (4K) would be placed around the floor, each with a wide field of view. With high resolution, you can use a digital zoom to focus in on a point of interest at some later time. If the cameras have overlapping fields of view, it is likely that most activities will be visible on one camera or another, or possibly on several at the same time.
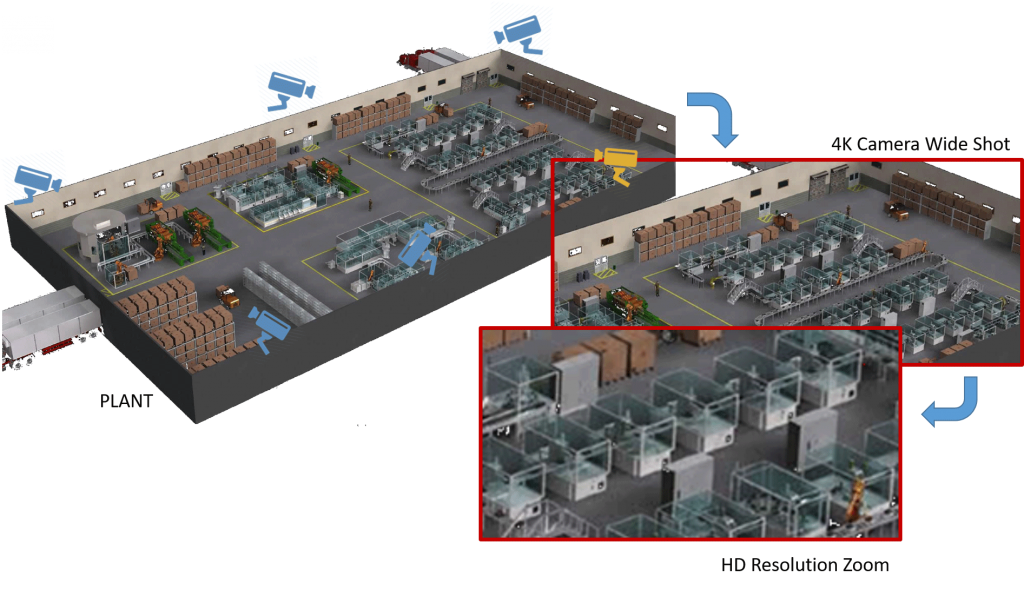
Plant management probably already know which points interest merit a more scrutiny, so inexpensive HD cameras can be installed in front of key machines and operations, possibly with a microphone. One camera might focus on the machine tool’s control panel. Another might take a wider view to see how the operator interacted with the panel and the machine. Together, they would capture most of the important actions in and around the machine.
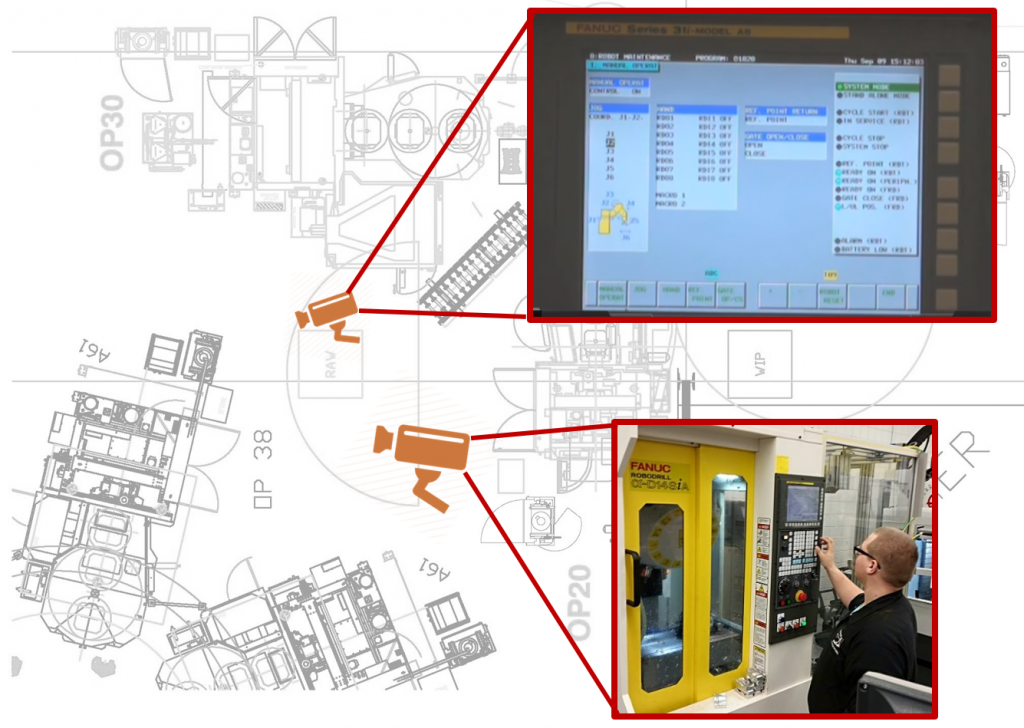
All of the different camera feeds come together on a common recording device, with a common timeline. The timeline is crucial. With all of the feeds synchronized, we can look at any point in time from as many viewpoints as we have cameras. If something happened, there is a very good chance that some camera (or combination of cameras) will have seen something useful.
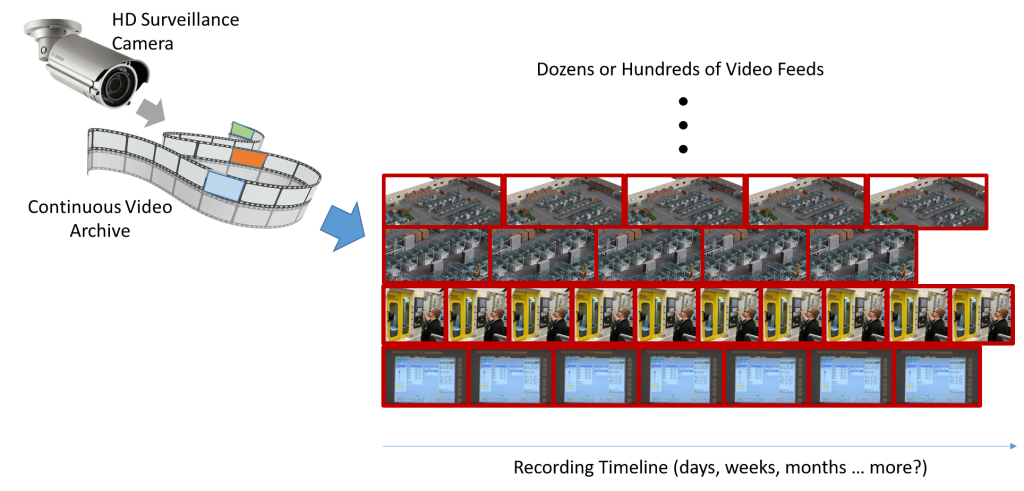
Think about the knowledge embedded in a video library like this. Somewhere, on some camera feed, there could be incontrovertible, measurable evidence of things like the following:
- How intermittent or rare process event actually transpired, from several camera angles and possibly with sound.
- How the settings on a machine tool control panel changed over time. Was there a warning that was ignored? Did the operator do the task in the same way?
- How materials actually moved through the process. Were units sidelined and delayed?
- How process flow times actually happened. Is movement regular and consistent, or are there odd happenings and outliers?
- How machines actually seemed to be running. Were cuttings what you expected? Did the operator have to fiddle with settings a lot?
- etc. etc. etc.
Finally, consider the history of manufacturing systems and innovations … ask how the pioneers might have done things differently if this sort of system were available:
- Gilbreth – “Finding the best way” – How would the Gilbreths have used a system like this to analyze best practice?
- Shewhart – “Statistical Quality Control” – Would Walter Shewhart have conceived of his control charts the same way if he had this as a tool?
- Deming – “Variation is the key” – How would W. Edward Deming have used a system like this to study process variation?
- Imai – “Continuous Improvement” – How would Masaaki Imai have used this capability to empower his Kaizen teams?
- Ohno – “Hunting Waste” – How would Taichi Ohno have mined the videos to seek and destroy Muda?
They didn’t have this technology, so they invented marvelously pragmatic tools to understand process history and isolate root causes … but what would they have recommended if they could view a video record of all prior production? My guess is they might have come up with something a bit different.
This is our time. This is our technical opportunity. What can we do with this capability? Or am I the only person who thinks this might be exciting?
Last point. This post is a teaser. If you build a system like this, it will open up a new world of knowledge and data. How will you handle that? What can you do with the information? It looks like we will need entirely new analysis and management tools to fully capitalize on this.